Inspection of the lithium surface by VacuumCIS possible!
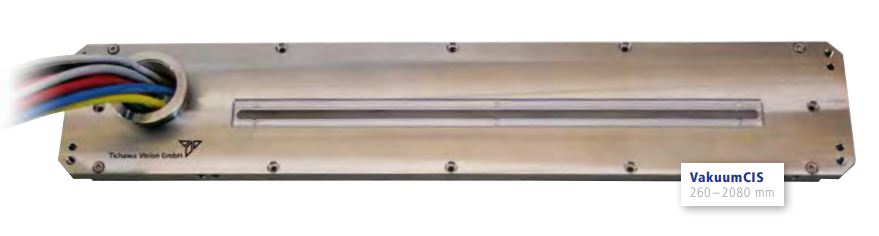
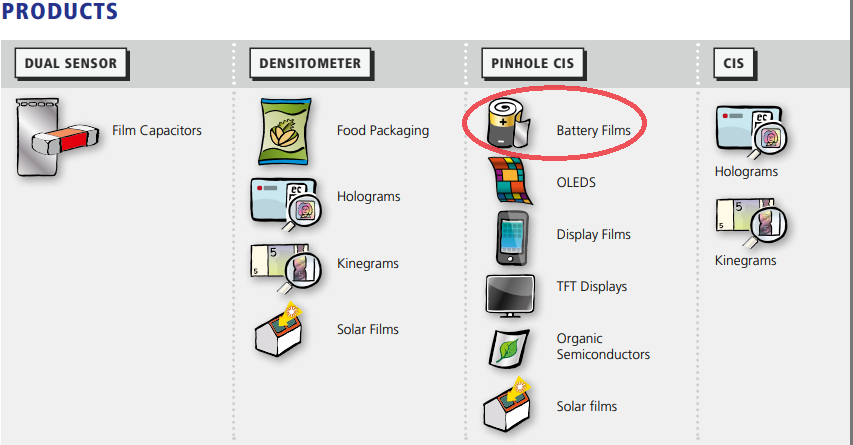
Battery films are extremely thin, flexible and conductive materials used in batteries to maintain the various layers of insulation and electrical contact between the components. They typically consist of several layers, including a conductive layer, a separator layer and a protective layer.
Defects in battery films can have various causes, including mechanical damage during manufacture or transport, chemical reactions with the electrolytes in the battery or thermal stress. Possible defects include cracks, holes, delamination (detachment of layers) and short circuits. If defects occur in the battery foil, this can impair the performance and safety of the battery. Short circuits, for example, can lead to overheating, fires or even explosions. It is therefore important to use high-quality battery foils and to carry out regular quality checks in order to recognise and rectify defects.
Do you want to detect defects on your battery foil to prevent complaints from you or your customers? Do you want to sort out your rejects by quickly recognising defects during production? With our CIS technology, our expertise and our wide range of lighting options, we can offer you a suitable solution to ensure the quality of your production in multiple ways. Our Shape-from-Shading illumination variant enables the detection of defects on light or dark battery foil. We also use our CIS to visualise all defects in both the longitudinal and transverse direction.
The graphite side of a battery foil is usually inspected. But how can the oxygen- and liquid-sensitive lithium surface be accurately inspected? With our VacuumCIS, a problem-free 2-in-1 solution is possible to scan not only the graphite side but also the lithium side of the battery foil.